Home
List your patent
My account
Help
Support us
Machine for the layered production of three-dimensional objects
[Category : - OTHER]
[Viewed 1070 times]
DE202019002699U1
The invention described herein is a machine for the layered production of three-dimensional objects using the fused filament fabrication method, which is also known as Fused Deposition Modeling (trade name Stratasys Inc.) method or in German as a melt layer method.
For the production of three-dimensional objects using additive manufacturing or 3D printing, a variety of different methods are available. One method that is especially popular for making three-dimensional plastic objects is the fused filament fabrication process. The method is also used for the production of three-dimensional objects made of metal.
In all additive manufacturing processes, a three-dimensional object is often first created on a computer using computer aided design (CAD) or computer aided manufacturing (CAM). Then, the three-dimensional object is exported to a file format for describing discrete surfaces. Such formats are z. STL, AMF or 3MF. In order to enable the layered production, the three-dimensional object must be cut into several layers. The layer thickness of each cut corresponds to the layer thickness of the horizontal layers to be produced. In machines of conventional design, the cuts are made horizontally to the global gravitational vector. All layers are parallel to each other. After cutting the three-dimensional object, a file is created that contains the cut information of the individual layers as well as travels and speeds of the print head and the build platform. This file can be transferred to the additive manufacturing machine, which uses the information contained to build up the three-dimensional object in layers.
Machines of conventional design which use the fused filament fabrication method have a movable construction platform on which the first horizontal layer of the three-dimensional object is produced. The direction of movement of the building platform is called along the direction of the global gravitational vector, often Z-direction.
The layers of the three-dimensional object are applied by at least one print head, which moves in both directions perpendicular to the movement direction of the construction platform, often called X-direction and Y-direction, and thus produces a complete horizontal layer of the three-dimensional object. The print head draws a wire-like material, usually plastic, plastic with metal particles or wax, liquefies it and extrudes the liquefied material by means of a nozzle. The liquefied material cures by cooling at the desired position and forms part of the horizontal layer to be produced. The movement of the print head establishes a complete horizontal layer of the three-dimensional object. After completion of a horizontal layer, the build platform moves one layer thickness and the next layer is produced. As an alternative to a mobile build platform, it is also possible that the print head performs the movements in the X, Y and Z directions. The build platform is immobile in this case. The movement of the printhead, the extrusion speed of the printhead and the movement of the build platform are controlled fully automatically by means of a computer unit. US Pat. 5,121,329 describes for the first time a machine and the method of fused filament fabrication.
Conventional-type machines using the fused filament fabrication process set a practical limit on productivity, as only one horizontal layer at a time can be produced after the other. The production of the three-dimensional object is thus a serial process. The limit of productivity is determined primarily by the extrusion and movement speed of the printhead. The higher the speed of extrusion and movement of the printhead, the faster the individual horizontal layers can be made and the higher the productivity of the machine. In CN108312514A describes a machine in which multiple printheads simultaneously make a single horizontal layer. Although this machine increases the productivity, but only for three-dimensional objects from a certain size. Below this size, the printheads can not work collision-free at the same time due to the necessary freedom of movement. In addition, the described machine can not scale arbitrarily in width and length, because otherwise not all locations of the build platform can be reached by the printheads.
This would particularly affect the locations in the middle of the construction platform. Thus, the in CN108312514A described machine rather for smaller construction platforms and thus also smaller three-dimensional objects used.
In W02015175651A1 For example, a machine and a method are described in order to be able to produce large areas of a single horizontal layer in parallel or a complete horizontal layer in one work step. This requires a print head, which may correspond to the entire length and width of the build platform. If the printhead does not match the entire length and width of the build platform, the printhead must be movable to fabricate anywhere on the build platform. This can lead to an enormous space requirement of the machine. Furthermore, a complex and thus error-prone control, regulation and material supply are necessary for the described machine to heat the material at each location of the build platform at the correct time to the required temperature and to extrude at the correct position. The material is extruded by means of a large number of small nozzles arranged in a horizontal grid. Thus, the material can be applied only at certain intervals, resulting in a discretization of the three-dimensional object in the horizontal plane and poor manufacturing qualities.
For machines of conventional design, which work according to the fused filament fabrication method, depending on the shape and orientation of the three-dimensional object support structures must be used. Among other things, support structures prevent excessive distortion and, if the overhangs are too large, form a firm base for the next horizontal layer to be produced and thus prevent a sinking of parts of the next horizontal layer to be produced. The use of support structures increases the printing time and the volume of the manufactured material and thereby the manufacturing cost of the three-dimensional object. It is therefore always desirable to minimize the support structure volume used in order to minimize the printing time and the production costs.
Support structures in the fused filament fabrication process are made from either the same material and the same printhead as the three-dimensional object or from a different material using a second printhead. After the completion of the three-dimensional object, the support structures are removed again and therefore have no further function for the finished three-dimensional object. By removing the support structures, further costs are incurred, which can also be minimized by minimizing the support structure volume. In WO2018186072A1 For example, a machine and method is described in which a second printhead is employed to exclusively manufacture the support structures from a material different from the material of the three-dimensional object.
The layered production of the three-dimensional object, in which all layers run parallel to each other and to the construction platform, strongly favors the above-mentioned problems by large overhangs or is the cause of delays. A minimization of support structures and distortion would be possible if the layers to be produced would not only run parallel to one another, but could also be produced perpendicular to one another and to the construction platform. In the production of layers perpendicular to the construction platform, the resulting overhangs are low enough and require no support structures.
With the invention it is achieved that a maximum of five layers can be produced simultaneously or independently. This enormously increases the productivity of the additive manufacturing machine. Furthermore, it is achieved with the invention that layers can be made arbitrarily perpendicular to each other. This is made possible by using at least five printheads that can move independently and each have their own drives and guides. One printhead moves in the XY plane, two printheads in the YZ plane, and two printheads in the ZX plane. The printheads in the YZ and ZX planes are opposite each other and allow layers to be made perpendicular to the build platform. As usual, the print head in the XY plane produces layers parallel to the build platform. By making five layers simultaneously or independently, the risk of collisions of the printheads is minimal.
The movement of the print heads, the extrusion speed of the print heads and the movement of the build platform are controlled fully automatically by a computer unit.
Financial informationI offer the described patent for complete sale. After a successful sale process, the patent will be transfered according to German law of the DPMA to the buyer. No costs will be charged for this process. After a successful transfer, the buyer owns all rights of the patent.
Patent publications:No publication
Asking price:
Make an offer
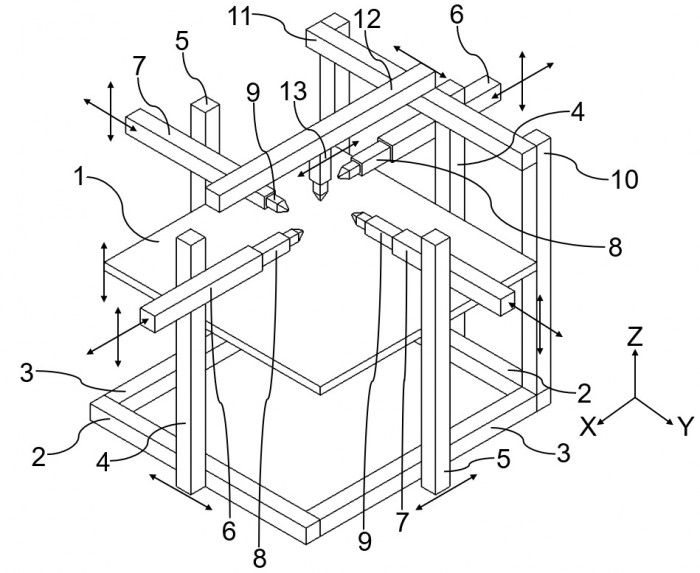
[ Home
| List a patent
| Manage your account
| F.A.Q.|Terms of use
| Contact us]
Copyright PatentAuction.com 2004-2017
Page created at 2025-08-21 5:39:50, Patent Auction Time.